Delivering quality
growing with customers
Striving to offer diverse one-stop service solutions through continuous.
How it works
How to choose electric vehicle high voltage connectors and wiring harnesses
Computer connectors are widely used in many scenarios, including
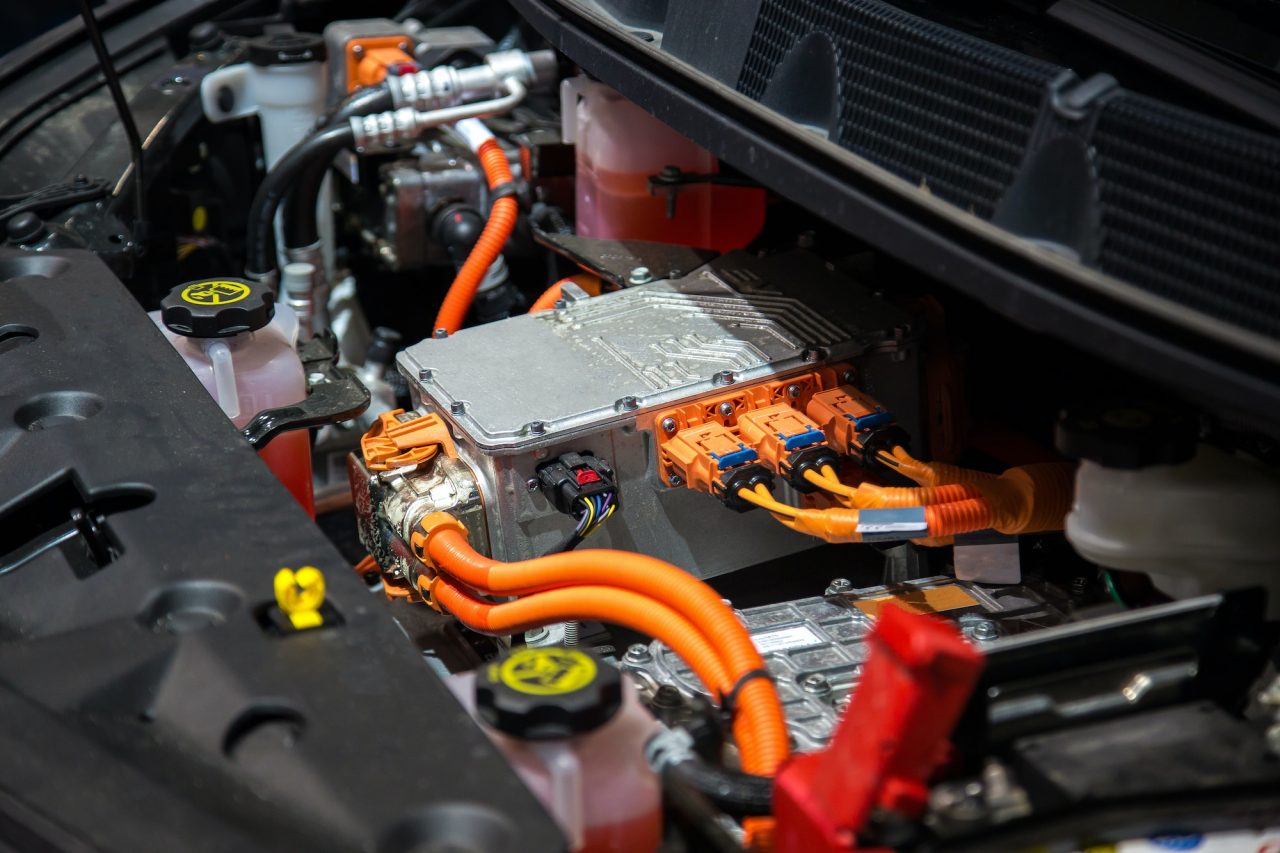
Overview
Automotive high-voltage wiring harness (high-voltage cable and high-voltage interface) is the key component of high-voltage electrical system, which provides guarantee for the reliable operation and safety of electric vehicles. The main development and design scheme of the vehicle high-voltage wiring harness involves cable layout, cable diameter selection, high-voltage connector selection, charging cable and interface type and application, cable fixing and protection.
The following points should be considered in the wiring harness arrangement:
Considering EMC electromagnetic interference factors, high-voltage cables should be shielded to avoid high-frequency noise emission. High – and low-voltage cables must be routed separately to avoid interference caused by overlapping wiring harnesses.
1. Consider the aesthetic layout of the wiring harness, and the direction needs to be consistent with the direction of the dependency, to avoid oblique. For the hatch wiring harness, as far as possible under or inside the structural parts or components, the bottom of the exposed high-pressure wiring harness of the vehicle is shielded by the tube protection plate and shielding plate.
2. Install and maintain the same part of the connector. Select different connector specifications and positioning methods to prevent misinsertion. The end of the connector must leave a certain amount of space for insertion and removal.
High voltage connector
Electrical performance: It is necessary to consider the rated working voltage, rated working current, insulation resistance, voltage rating, shielding and interlocking and other related electrical performance parameters.
Environmental performance: It is necessary to consider the requirements of working temperature, ambient temperature, salt spray grade, flame retardant grade, solution resistance reagents and prohibited substances.
Mechanical properties: Test vibration resistance and corresponding mechanical life according to different working conditions.
Safety performance: high voltage interlock has internal and external, the internal layout is compact, small size, the internal is used for electric vehicles, through VMS or BMS and other controllers to detect the high voltage interlock, after separating the high voltage connector, the live part must be reduced to 60Vd.c, 30Va.c below within 1S to ensure personal safety.
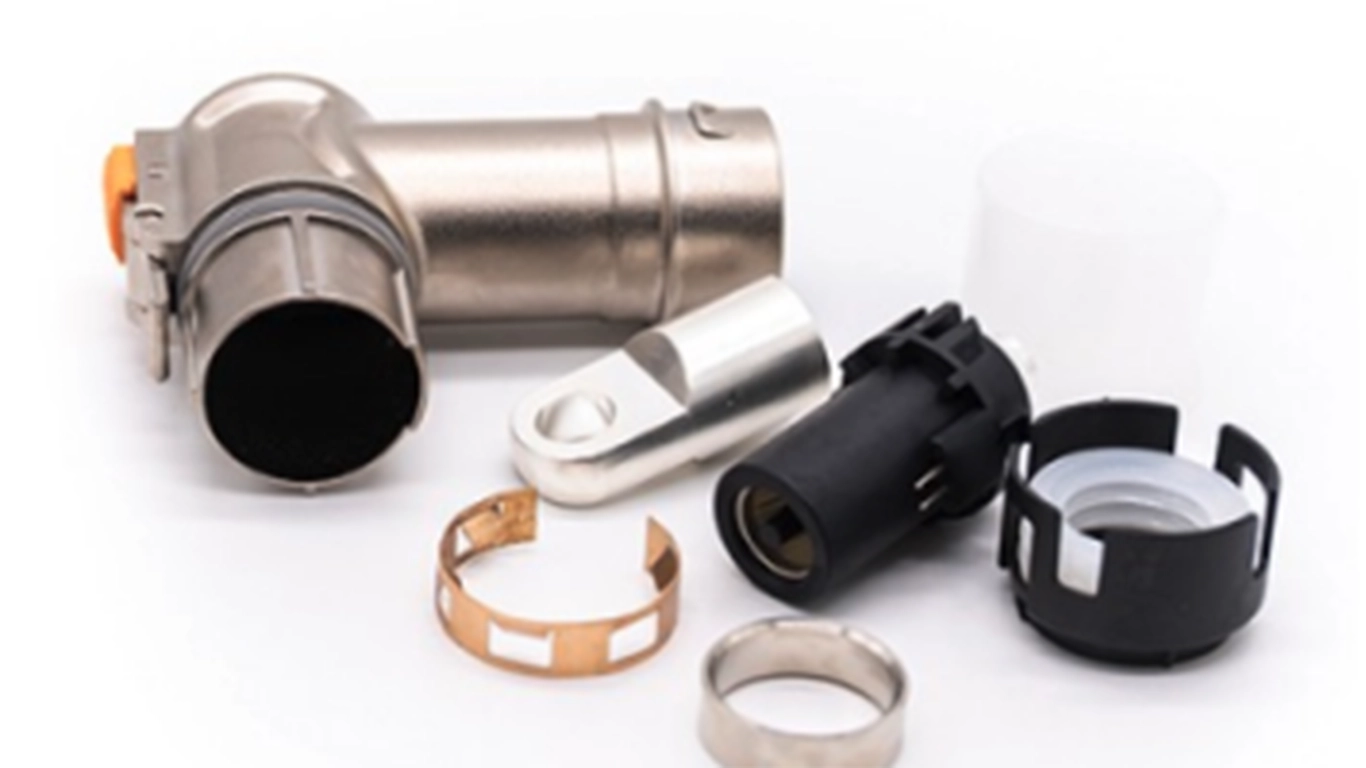
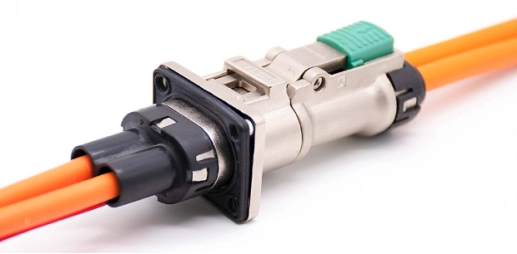
Charging interface
At present, there are two kinds of charging interfaces: AC and DC. The AC interface connects the electric energy of AC network to the vehicle charger through the control and protection device on the cable. The DC interface is a power supply device that directly controls and switches the electric vehicle battery.
The rated AC port voltage is 250Va.c or 440Va.c, and the rated current does not exceed 63A. The rated voltage of the DC interface is 750Vd.c or 1000Vd.c, and the rated current does not exceed 250A. The rated voltage and current value of the charging interface shall be determined according to the vehicle layout requirements. Other relevant electrical characteristics and other AC-DC charging interface parameters must meet the requirements of the national standards GBT20234.2-2015 and GBT20234.3-2015.
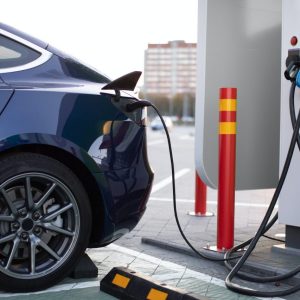
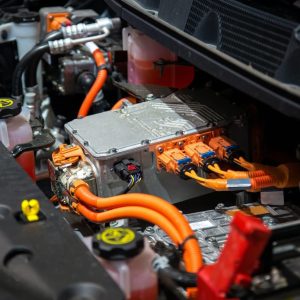
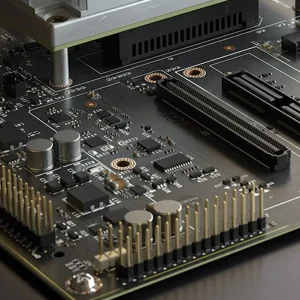
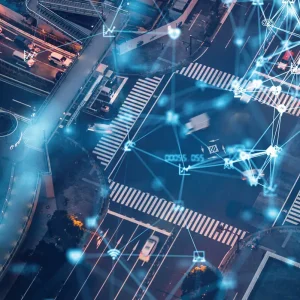
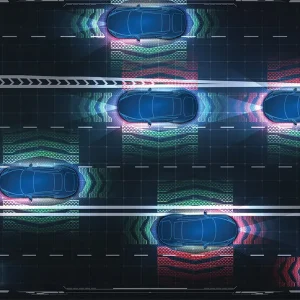
Custom Order > Solution Communication > Software Simulation > Multi-Party Review > Finalize Design and Mold Making
Choose Fujinying 4 Reasons
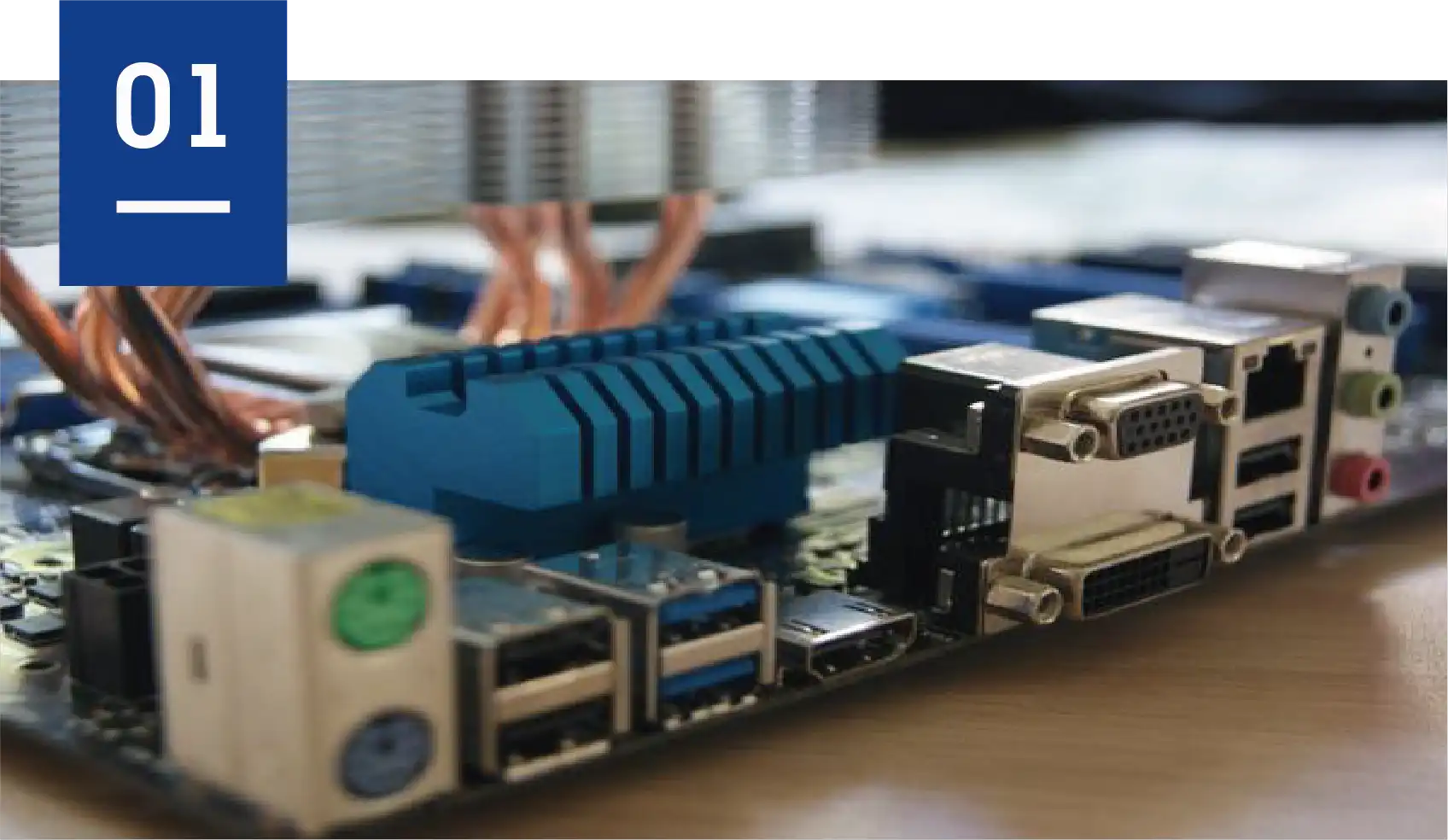
Professional solution, customized
Experienced engineering team – Professional, efficient, reliable.
- Development focuses on customer needs, with dedicated engineers coordinating projects and conducting multi-angle design reviews;
- We use effective design tools like Pro-E, SolidWorks, AutoCAD, and ABAQUS;
- Our engineering team averages 10 years of experience in the connector industry;
- Automation is integrated into the product design phase to ensure quality and production capacity.
Full automation to ensure capacity
20 years of custom R&D for high-quality connectors, optimizing production lines.
- Over 500 automated assembly machines.
- Global automation design to free up labor and enhance efficiency.
- Minimized capacity drops from labor turnover.
- A team of skilled professionals continuously optimizes production lines and actively adopts automation technologies to improve capacity and quality.
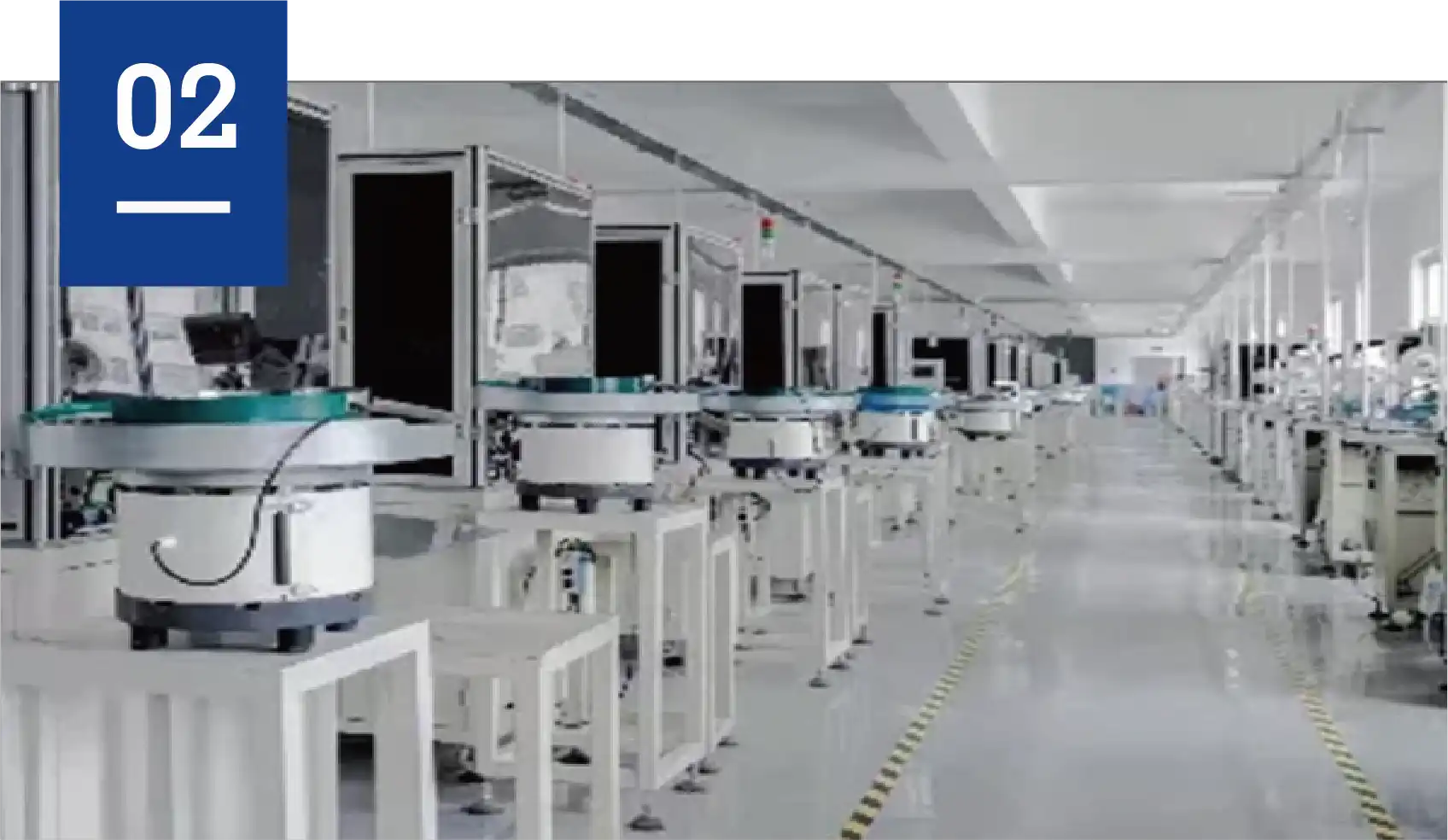
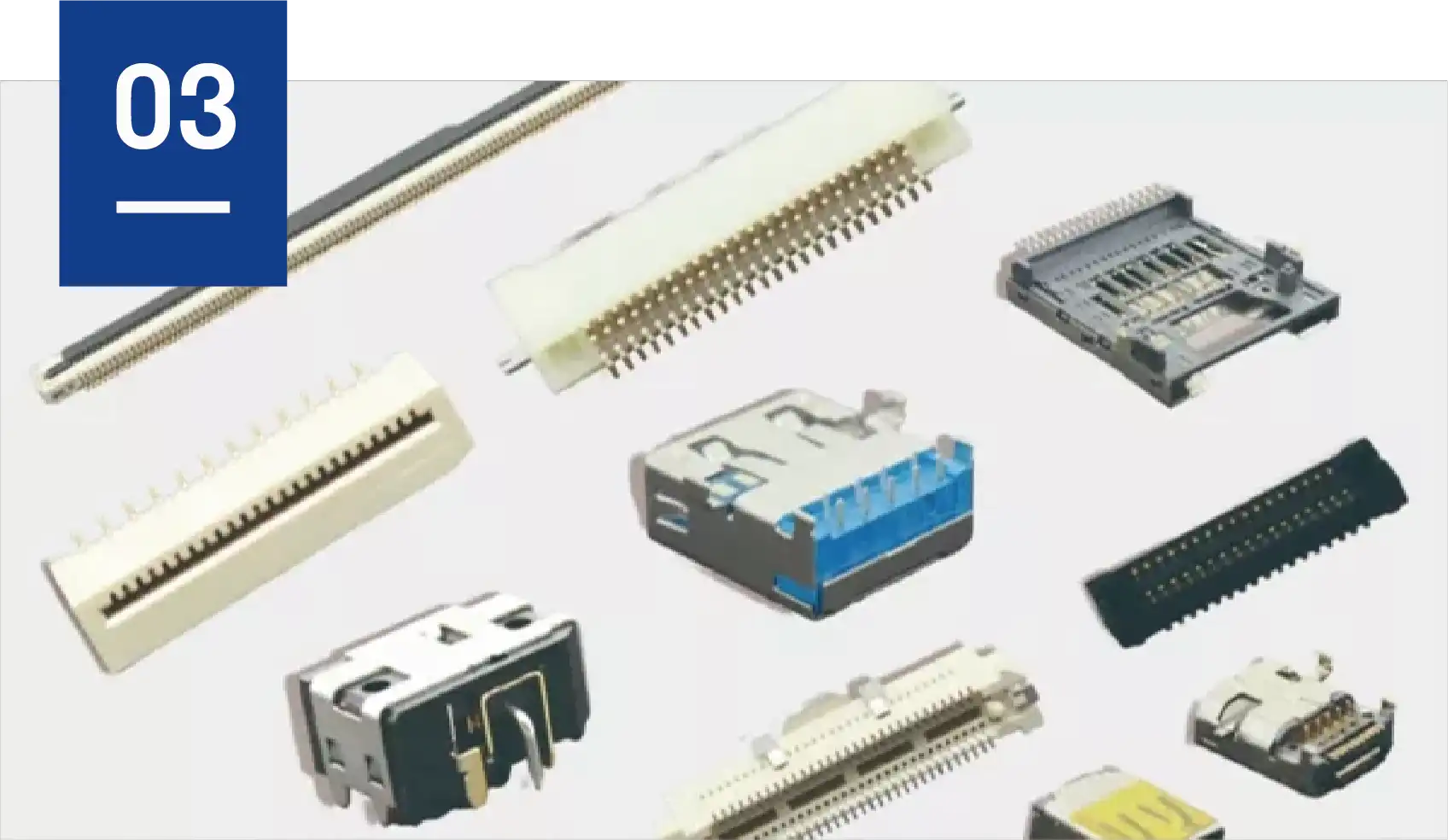
Strict manufacturing processes
Widely recognized by many renowned global companies.
- Mitigate quality risks from the product design phase;
- Ensure quality through global automated production and data monitoring;
- Guarantee that every connector meets standards and customer requirements;
- Robust quality assurance system, complete testing equipment, and data-driven quality monitoring.
Wide variety, broad applications
Customizable to meet various needs, making one-stop connector procurement easy!
- 10 categories of connectors with over 50 series and thousands of models;
- Widely used in computers, communications, AI, digital products, audio-visual equipment, and security devices;
- Dedicated to creating a one-stop connector service system to be the most professional connector solution manufacturer.
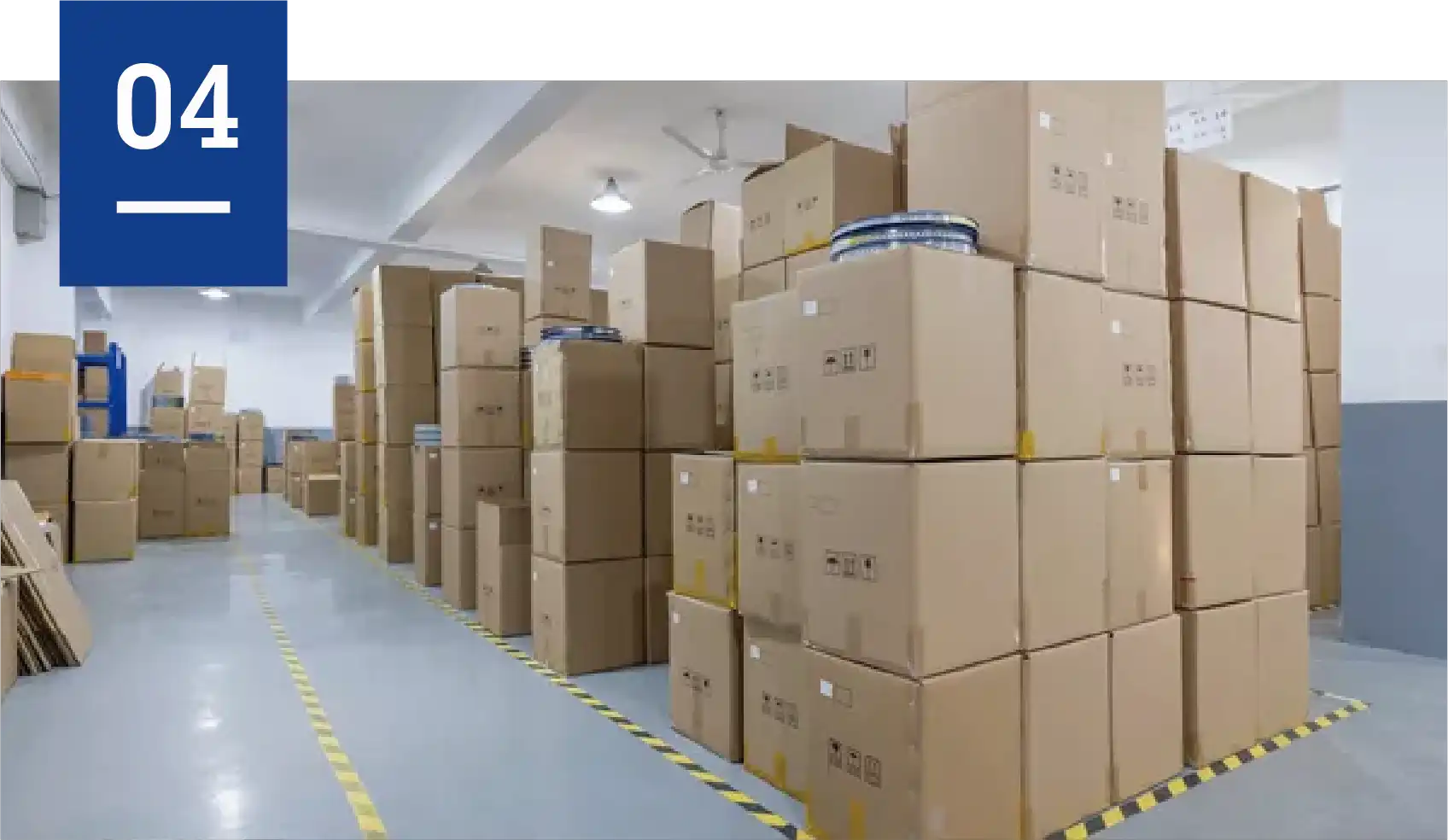
Connector connections are trustworthy,Tell me what you want !
Shenzhen Fuyinjing Electronics Co., Ltd.
is a leading connector manufacturer committed to providing high-quality solutions.